Intro to welding and types of welding
- SkillCat Team
- Mar 27
- 8 min read
Intro to Welding: Chapter 1
Introduction to Welding
By the end of this module, you should be able to:
Describe what welding is
Explain the importance of welding
Describe the history of welding. Skip to quiz!
Welding
Welding is the process of joining two pieces of metal together to form one piece by heating the metals to their melting points. Sometimes filler metal is used to help bond the two pieces together. A filler metal is an additional metal used to secure a joint through welding.
Welding uses high temperatures to fuse the base metals by melting them. There are other methods of fusing metals, such as brazing and soldering, which use lower temperatures and do not melt the base metal (parent metal). If you want to know more, there is a separate course on Brazing and Soldering.
Why is welding important?
How does welding appear in the products we use daily?
How does welding make our lives easier?
Let’s discover some answers to these questions.
Welding is an essential component of many manufacturing industries. Without this form of metalwork, many things - buildings, gates, kitchen appliances, motor vehicles, and even space travel - would not exist.
Welding provides strong and permanent joints for structures. It is essential for any manufacturing operation, such as the automotive and aviation industries. Welding is also used in the building of structures, making it the backbone of the construction industry.
Research from the American Welding Society suggests approximately 70 percent of all manufactured products are manufactured using welding skills. It is solid evidence of the importance of welding to the economic health of the United States. Joining two pieces of metal together is difficult, but welding makes it easier by making those metal joints strong and permanent.
The welding trade presents many challenges, so knowledge of its specialized safety equipment and tools is vital. To practice welding safely and with skill, it is important to get a lot of practice, more so than many other types of work. Let’s watch a video on a day in the life of a welder.
History – Origin of Welding
Metalworking is an ancient practice. The first welding techniques appeared in the Iron Age, 7 to 8 thousand years ago. Between 2000 BC & 3000 BC, small gold circular boxes were made by pressure welding lap joints together.
Forge welding is the practice of heating metal until it glows and becomes soft. Heated pieces can then be fused by pounding. Forge welding first appeared around 1800 BC. Forge welding was used to build an Iron Pillar in Delhi, India around 310 AD. It was also used for making jewelry and weapons for the rich.

Forge welding is not the earliest known form of welding, but it was the first welding process that brought welding to the “masses.” Things like plows, cutting tools, and other tools could now be fashioned for farmers and other working people.
In 1800, Sir Humphry Davy, a British chemist, formed the first electric arc between two carbon electrodes. His accomplishment inspired all of the forms of arc welding that followed.
Acetylene was discovered by Edmund Davy in 1836, providing a controllable heat source for welding and cutting. Using acetylene for welding was impractical until about 1900 when the first blowtorch was developed. It was the start of oxyfuel welding and cutting. This method is still used today, mostly for cutting metal.
In 1890, C.L. Coffin of Detroit was awarded the first U.S. patent for an arc welding process using a metal electrode. It was the first record of a weld made using metal melted from an electrode and carried over an arc to deposit filler metal in a joint.
In the same era, other welding processes were being developed. Resistance welding originated from inventor, Elihu Thompson. His patents were dated 1885-1900. Hans Goldschmidt invented thermite welding. Thermite welding was initially used to weld railroad rails in 1903.
Until the end of the 19th century, the only welding process was forge welding, which blacksmiths had used for millennia to join iron and steel by heating and hammering. In 1919, the American Welding Society was founded by 20 members of the Wartime Welding Committee of the Emergency Fleet Corporation, under the leadership of Comfort Avery Adams.
Welding technology advanced quickly during the early 20th century as world wars drove demand for reliable and inexpensive joining methods. Several modern welding techniques were developed in this era, including manual methods like shielded metal arc welding, gas metal arc welding, submerged arc welding, flux-cored arc welding, and electroslag welding.
Welding is the process of permanently joining two metals, using various methods. Welding was developed in early times. Forge welding was the main method used for a long period of time. Welding technology advanced quickly during the early 20th century as world wars drove the demand for reliable and inexpensive joining methods.
Types of Welding - Part 1
By the end of this module, you should be able to:
Describe different types of welding
Explain some of the commonly used welding processes. Skip to quiz!
Types
There are several types of welding. The welding type is determined by the job requirements and the type of technology used.
Welding types fit into one of two categories:
Plastic welding
Fusion welding
Plastic welding or pressure welding is the process by which pieces of metal to be joined are heated to a plastic state and then forced together by external pressure. This welding process is also known as liquid-solid welding. This method is used in both forge welding and resistance welding.
Fusion welding or no-pressure welding is the process by which material at the joint is heated to a molten state and allowed to solidify. This welding process is also known as liquid state welding. It is used in gas welding, arc welding, thermite welding, and other welding types.
Some of the most common welding methods include:
Gas Welding
Arc Welding
Resistance Welding
Electron Beam Welding
Let’s look at these in more detail.
Gas Welding
Gas welding is one of the oldest and most versatile welding processes. There are many types of gas welding processes, but the most common is oxyfuel welding, also known as oxyacetylene welding. It is still widely used for welding pipes and tubes and repair work.
The equipment used is relatively inexpensive and simple. Generally employing the combustion of acetylene in oxygen to produce a welding flame temperature of about 3100 °C (5600 °F). It is less concentrated than an electric arc.
The flame causes slower weld cooling, which can lead to greater residual stresses and weld distortion, though it eases the welding of high alloy steels. A similar process, generally called oxyfuel cutting, is used to cut metals. Different kinds of filler metals are used as per base metals.
Arc Welding
Arc welding uses an electric power supply to create and maintain an electric arc between an electrode and the base material to melt metals at the welding point. It can use either direct current (DC) or alternating current (AC), and consumable or non-consumable electrodes.
The welding region is sometimes protected by some type of inert or semi-inert gas, known as a shielding gas. Filler material is sometimes used as well. Inert gases are those that do not react with gases in the atmosphere around the welding. There are many types of arc welding. Let’s review some common types.
One of the most common types of arc welding is shielded metal arc welding (SMAW). It is also known as manual metal arc welding (MMAW) or stick welding. In stick welding, an electric current is used to strike an arc between the base material and consumable electrode rod made of a filler material, typically steel.
The rod is covered with a flux that protects the weld area from oxidation and contamination. It does this by producing carbon dioxide gas (CO2) during the welding process. The electrode core itself acts as filler material, making a separate filler unnecessary.
Gas metal arc welding (GMAW) is also known as Metal Inert Gas or MIG welding. This process uses a continuous wire feed as an electrode, and an inert or semi-inert gas mixture to protect the weld from contamination. Due to the continuous electrode, the welding speed is greater than others.
Gas tungsten arc welding (GTAW) is also known as tungsten inert gas or (TIG) welding. This is a manual welding process that uses a non-consumable tungsten electrode, an inert or semi-inert gas mixture, and a separate filler material.
Resistance Welding
Resistance welding generates heat by passing current through the resistance caused by contact between two or more metal surfaces. As a high amperage current (1,000 -100,000 A) passes through the metal, small pools of molten metal are formed at the weld area.
In general, resistance welding methods are efficient and cause little pollution, but their applications are somewhat limited and the equipment cost can be high. Spot welding is a popular resistance welding method used to join overlapping metal sheets up to 3 mm thick.
Two electrodes are simultaneously used to clamp the metal sheets together and to pass current through the sheets. The advantages of the method include efficient energy use, limited workpiece deformation, high production rates, easy automation, and no required filler materials.
Weld strength is significantly lower than with other welding methods, making the process suitable only for certain applications. Resistance welding is used extensively in the automotive industry. A single car may have several thousand spot welds made by industrial robots.
Energy Beam Welding
Energy beam welding methods are laser beam welding and electron beam welding. These are relatively new processes that have become quite popular in high production applications. The two processes are quite similar, differing most notably in their source of power.
Laser beam welding employs a highly focused laser beam, while electron beam welding is done in a vacuum and uses an electron beam. Both have a very high energy density, making deep weld penetration possible and minimizing the size of the weld area.
Both processes are extremely fast, and are easily automated, making them highly productive. The primary disadvantages are their very high equipment costs and a susceptibility to thermal cracking.
There are several types of welding. The welding type is determined by the job requirements and the type of technology used.
Welding is mainly divided into two types and their subdivisions.
Plastic welding
Fusion welding
Common welding types include gas, stick, MIG, TIG, and energy beam welding.
Question #1: What is the process of joining two metals?
Molding
Fixing
Welding
Hammering
Scroll down for the answer...
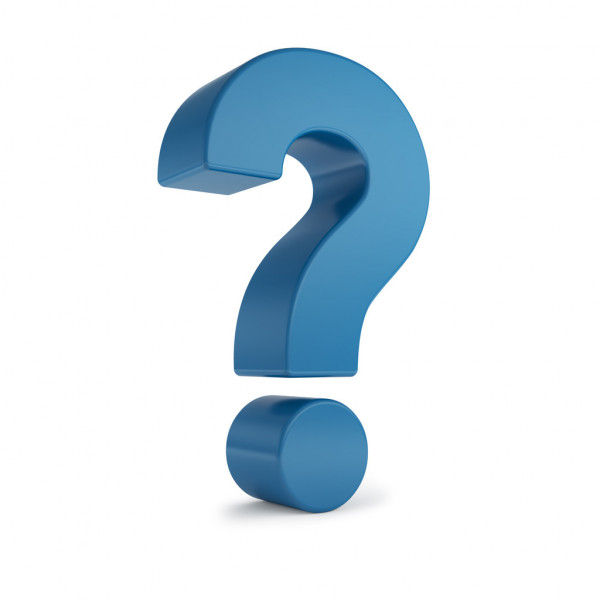
Answer: Welding
The process of joining two metals is known as welding.
Question #2: Which type of welding was used in ancient times?
Forge welding
Heat welding
Oil welding
Coil welding
Scroll down for the answer...
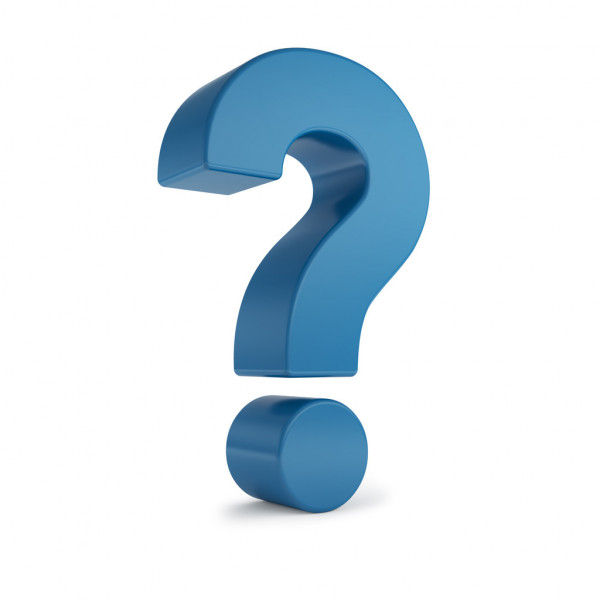
Answer: Forge welding
Forge welding has been used since ancient times.
Question #3:Select different types of welding. (Select all the answers)
Arc welding
Tube welding
Laser welding
Light welding
Scroll down for the answer...
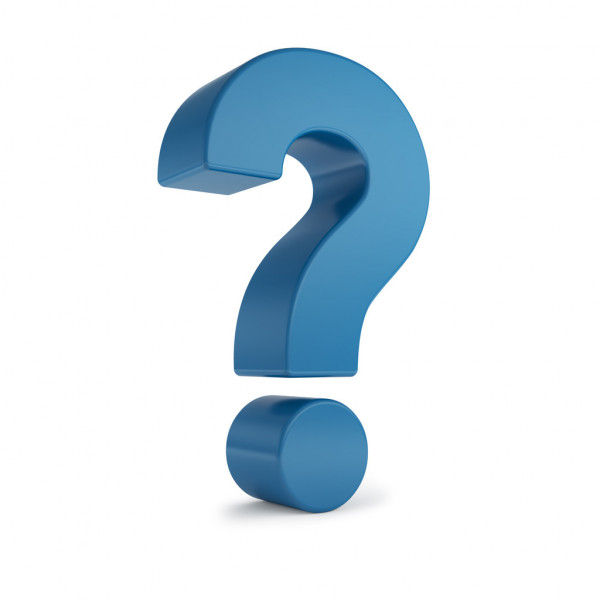
Answer: Arc welding and Laser welding
Types of welding include arc welding, resistance welding, laser welding, and friction welding.
Question #4: Which types of gas are used in gas welding?_____.
Oxygen and Acetylene
Carbon and Hydrogen
Hydrogen and Oxygen
Nitrogen and Oxygen
Scroll down for the answer...
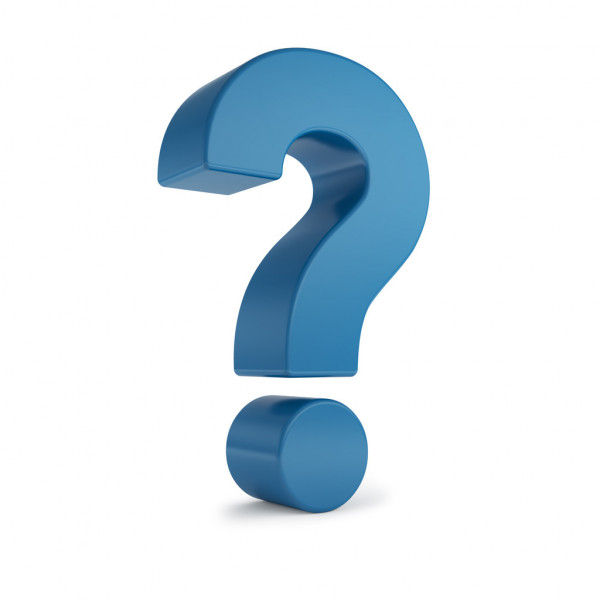
Answer: Oxygen and Acetylene
Oxygen and Acetylene gases are used in gas welding.
Question #5: How are metals arranged during resistance welding?
Kept apart
Kept in contact
Kept aside
Kept near
Scroll down for the answer...
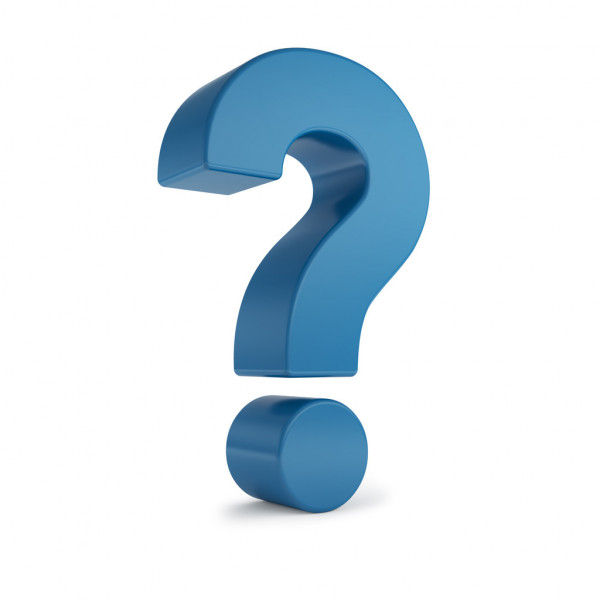
Answer: Kept in contact
Metals are kept in contact during resistance welding.
Other References: