Compressor Overhaul, Condenser Overhauls, & Evaporator Overhauls
- SkillCat Team
- Apr 8
- 11 min read
Seasonal Overhauls for Chillers: Chapter 2
Compressor Overhaul
You made sure chillers were properly laid up, treated, and then drained before shutdown. Good job! But have you ever wondered how to overhaul a compressor? It's not as simple as maintaining a daily log. This module will help you to understand how to overhaul a compressor. Skip to quiz!
Introduction
A chiller produces cold water by using the basic refrigeration cycle. Recall that the main components of a refrigeration cycle are:
Condensers,
Metering devices,
Evaporators, and
Compressors.
Every component of the chiller system plays an important role. We need to maintain all of them during seasonal overhaul to ensure efficient operation during peak demand months.
Compressor Overhaul
We need to inspect compressor components for signs of a leak and wear visually during compressor overhauling. The goal is to identify deficiencies that we can address during the shutdown.
If we find signs of corrosion while inspecting, we should apply anti-corrosives. If the damage is not repairable, we need to replace the component. This is similar to replacing rusty beams of a building if they are not repairable.
Think about your motorcycle chain. It has rubber seals sandwiched between the side plates and internal links. If these seals get damaged or loose, they can't lubricate chains. In the same way, broken seals on your compressor are useless. If damaged, replace critical components like gaskets, O-rings, covers, and seals.
When the compressor is disassembled for service work, visually inspect the bearings, gears, and shaft seals. The key to good maintenance of these components is proper lubrication. Ensure that the proper grade of oil is maintained at the recommended level.
Observe the compressor oil through the sight glass. The compressor oil should be between the high-level and low-level lines.
If the oil level falls below recommended, we will add oil to a compressor oil reservoir using a vacuum pump.
Before starting the oil filling process, we need to shut off the exhaust and suction valves. Then we open the needle valve to release the gas inside the compressor. By connecting the vacuum pump to the needle valve, we fill the oil from the oil can into the compressor until the oil sight glass fills up.
Another factor that can cause improper lubrication of chiller components is oil quality. Compressor oil will become dark if
mixed with refrigerant when a chiller system is operating, and
exposed to impurities
When the compressor oil has changed color or degraded quality, it must be changed.
For changing compressor oil, we follow the same procedure as oil filling. We then close exhaust and suction valves. Next, we open the needle valve to release the gas inside the compressor.
In case of an oil change, we need to drain out degraded oil inside a compressor. This is done by opening the oil discharge outlet screw. After removing all the oil, we tighten the oil discharge outlet screw.
Next, we connect the vacuum pump to the needle valve. This will create a vacuum inside the compressor and pull out oil from the oil can. After the oil is filled, we open the exhaust and suction valves.
Overhauling is also the time to verify:
proper operation of the oil or crankcase heaters,
ensuring oil filter is clean, and
checking for refrigerant level.
Let’s look at each of them in detail.
We also need to ensure that the oil filter is clean. If it is clogged, it can prevent oil circulation in the compressor.
To check the oil filter, open the filter head on the compressor. A dirty oil filter needs to be replaced. Replacing an oil filter on a chiller compressor is the same as changing your car filter.
Just like checking the oil level, we need to also check for refrigerant level. This is to ensure that no leaks are present in the system.
During winter shut down, refrigerant can mix with compressor oil and settle down to the bottom. Because of this, a chiller compressor would have to work a lot harder during startup. Crankcase heaters must be energized before startup to separate refrigerant from the oil.
To check the crankcase heater, measure its resistance. The circuit has continuity if the multimeter reads more than 0 ohms. If the circuit has continuity, then the crankcase heater is working fine.
There is no continuity if the meter displays "0L" while your leads touch. We need to replace a faulty crankcase heater during overhauling.
We need to inspect compressor components for wear corrosion and lubricate them during compressor overhauling. Overhauling is also the time to verify:
proper operation of the oil or crankcase heaters,
ensuring oil filter is clean, and
checking for refrigerant level.
Condenser Overhauls
We have said it before, and we’ll say it again: When the chiller is freshly shut down, it is the best time to clean, maintain and inspect it. The condenser is not an exception for this. This module will help you understand how the seasonal maintenance of your water-cooled and air-cooled condenser is worth the effort. Skip to quiz!
Water Cooled Chillers
Recall that a condenser’s main job is to cool down the refrigerant. Do you recall the type of condenser used in a water-cooled chiller? We use a shell and tube condenser. They are a series of copper tubes inside a shell.
Once it has been determined that the cooling system is no longer required for the winter, we drain off the water inside the chiller system. You need to inspect and clean soon after shutdown. Why?
Leaving condensers stagnant all winter waiting for a good time to drain them is inviting problems like freezing of water. The condenser should be left open until the next startup. This requires the removal of condenser end bells so that air can circulate freely through the tubes.
During this shutdown, windblown dust and dirt will permeate into condenser tubes. It’s much easier to remove it before it has caked on for the season. If it’s left in the tube for months, the possibility of corrosion multiplies exponentially, and it may cause serious problems.
For these reasons, you want to brush the tubes. Brush every single tube seasonally, even if they appear clean. You will be glad you did. This will reduce the risk of corrosion when the condenser is sitting idle for months.
Brushing the tubes removes any sludge or debris that may have settled inside tubes, We need to brush tubes as soon as possible after the fall shutdown. After cleaning the tubes, we need to inspect them for cracks.
We can detect visible cracks manually while overhauling. Eddy current testing (ECT) is an accurate means of determining the condition of tubes. Eddy current testing uses electromagnetic induction to identify defects in tubes.
Eddy Current Testing is one of the best tubing inspection methods because the probes are uniquely shaped to test chiller tubes. This probe generates a changing magnetic field. When we insert this probe into conducting tubing magnetic field causes eddy currents to flow in the tube.
The amount of eddy currents that can flow in the tube depends on the condition of the tube. These eddy currents will, in turn, generate a magnetic field that opposes the magnetic field of the probe coil. The resultant of these magnetic fields influence the current flowing through the coil.
The opposition to current flow is nothing but the impedance of the coil. This means the impedance of the test coil depends on the condition of the tube. These signals are presented on the ECT screen. These signals are compared with calibrated results to get test results
Before starting Eddy Current Test, we need to:
Shutdown the chiller if it is running,
Close the inlet and outlet valves of the condenser tube, and
Open an end bell of the condenser tube.
Next, we need to set up an eddy current machine near condenser tubes. To test the tubing, insert the probe inside each condenser tube along its entire length. If test results indicate cracks inside the tubing, then tube failure can result in chiller shut down in the future.
Detecting flaws on any tube can avert such failure and the accompanying shutdown. Keep in mind that once you identify a tube prone to failure, you can isolate that tube. It's unnecessary to replace the tube bundle when just a few tubes exhibit problems.
Air Cooled Chillers
Much like water-cooled condensers, dust and dirt will permeate during winter into these metal plates. This dust would likely be drawn into the condenser air intake filter or the condenser coil itself. Any accumulation of dirt, dust, and grime will cause progressive underperformance of chillers.
We need to clean the condensers during the seasonal overhaul to prevent underperformance. This will save energy bills due to the underperformance of chillers and save our money.
Before starting the cleaning, we first turn off the power supply to the chiller. Start spraying the tap water on the top of the air-cooled chiller and condenser fans with the help of jet spray. Next, we need to clean the condenser coils. Always clean in the opposite direction to the airflow.
Condenser coils should be washed in a manner that will not cause fin damage. We have to make sure that there is no debris on the condenser coils. Lastly, we have to clean the floor and the surroundings of the condenser.
During chiller shutdown, windblown dust and dirt will permeate into condenser tubes. We can detect fouling and scale formation visually while overhauling the water-cooled condenser. We can perform additional testing, like Eddy Current Testing (ECT).
Much like water-cooled condensers, dust and dirt will permeate during winter into these metal plates. We need to spray tap water on the air-cooled condenser to clean them.
Evaporator Overhauls
We’ve frequently emphasized the importance of cleaning your condenser tubes after you shut down your chiller in the last module. This module will help you understand how overhauling helps evaporator tubes last longer. Skip to quiz!
Evaporator
Recall that the purpose of the evaporator is to produce chilled water that is being circulated throughout the building. Do you recall the type of evaporator used in a water-cooled chiller? Much like a condenser, the evaporator used in a chiller is of shell and tube type.
Recall that temperature lowers during a winter shutdown. As we already discussed, draining water inside the chiller system will prevent the freezing of tubes.
We need to ensure that there is no water inside the evaporator during overhauling. Like condenser, evaporator end bells should be left open until the next startup.
If we found scale buildup inside evaporator tubes during overhaul, we need to clean them. This softens and breaks down scale deposits in the tubes. We follow the same procedure of cleaning condenser for evaporator cleaning.
For cleaning the shell and tube evaporator, we need to remove the front and back covers of the evaporator. Then we have to clean the evaporator tubes with the rodding machine.
While removing front and back covers, always check the condition of the gasket. If the gasket becomes harder or cracked, we need to replace it. If we do not replace the cracked gasket during overhaul, it will cause leakage.
Leakage can also occur if the evaporator tube is cracked. Eddy current testing (ECT) is an accurate means of determining the condition of both condenser and evaporator tubes. We need to isolate the defective tubes after analyzing ECT results.
During a seasonal shutdown, we drain off the water inside the evaporator. We need to clean the evaporator tubes to remove any debris inside the tubes. Lastly, test them to ensure that they are in good condition.
Question #1: What is the correct level of oil that needs to be maintained?
Half filled
Fully filled
Above centre line
Oil below centre line
Scroll down for the answer...
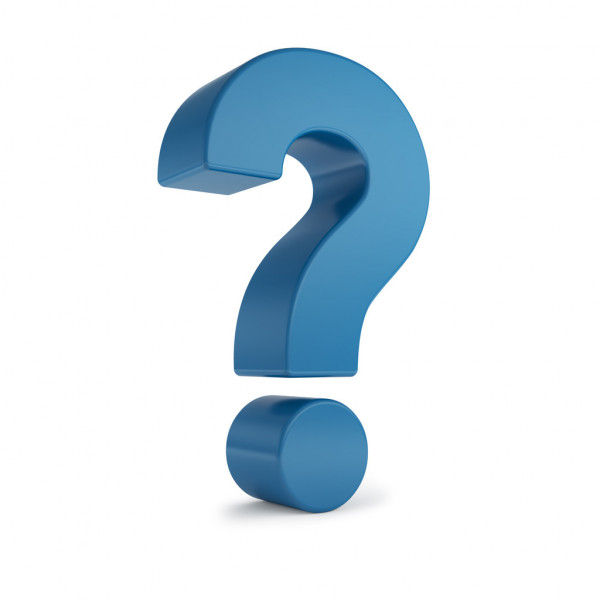
Answer: Half filled
The compressor oil should be between the high-level and low-level lines.
Question #2: What would you do if you found a drop in the compressor's oil level during the overhaul?
Lubricate bearing
Add oil
Change oil filter
Change motor.
Scroll down for the answer...
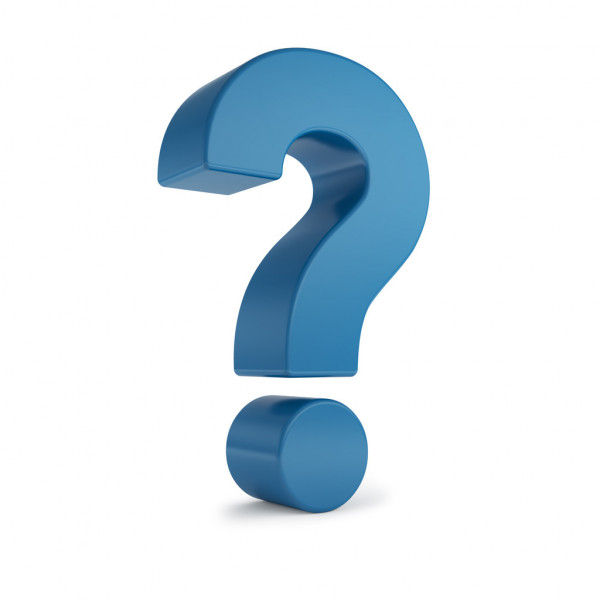
Answer: Add oil
We have to add oil to the compressor when the oil level drops below recommended.
Question #3: We have to change the compressor oil when it becomes ________ in color.
dark
white
green
blue
Scroll down for the answer...
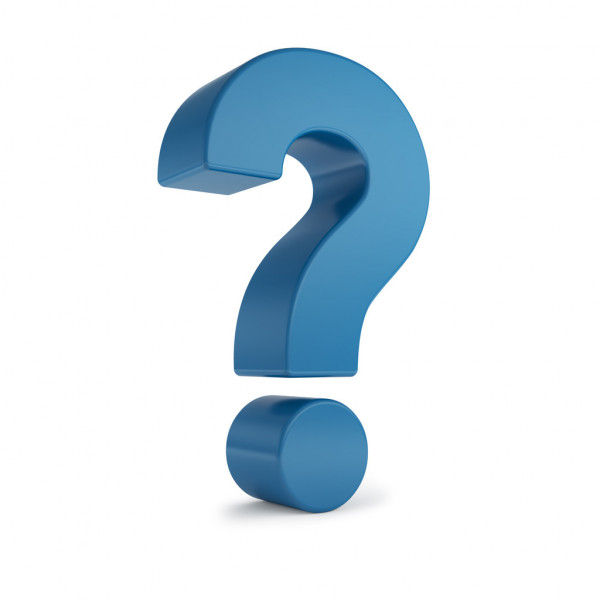
Answer: dark
We have to change the compressor oil when it becomes dark in color.
Question #4: What will you verify at the time of compressor overhauls? (select all that apply)
Oil filter
Operation of the oil or crankcase heaters
Refrigerant level
Drift eliminator
Scroll down for the answer...
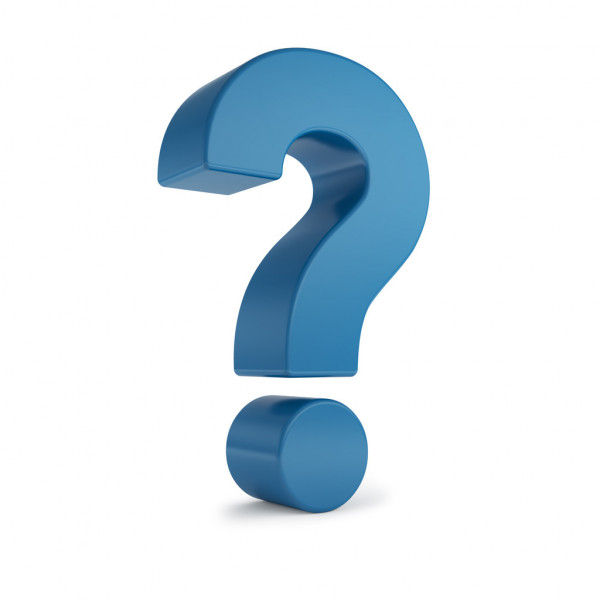
Answer: Oil filter
Operation of the oil or crankcase heaters
Refrigerant level
Overhauling is the time to verify: proper operation of the oil or crankcase heaters, ensuring oil filter is clean, and checking for refrigerant level.
Question #5: Which of the following prevents the circulation of oil in the compressor?
Dirty air filter
Clogged oil filter
Worn out impeller
Electric motor
Scroll down for the answer...
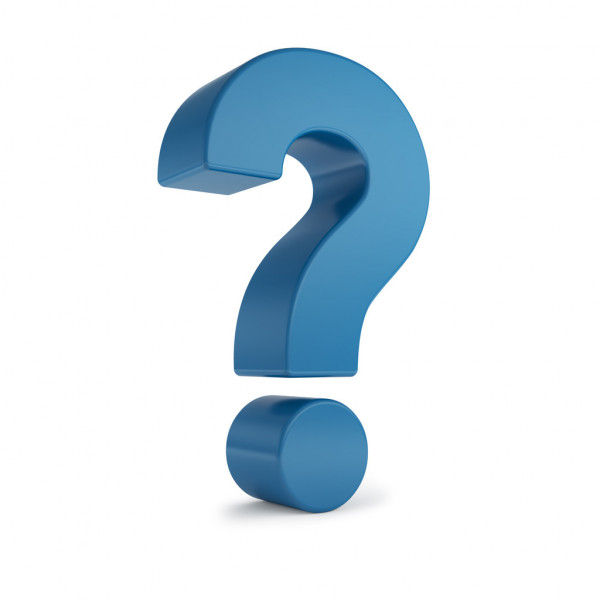
Answer: Clogged oil filter
A clogged oil filter prevents the circulation of oil in the compressor.
Question #6: How do we verify the operation of the crankcase heater during overhauling?
Checking its temperature
Checking conductivity
Checking resistance
Checking pressure
Scroll down for the answer...

Answer: Checking resistance
To verify the operation of the crankcase heater, we check the resistance of the heater.
Question #7: Why do we need to remove water from the chiller condenser immediately after shutting down?
To inspect the tubes.
The water inside tubes can freeze in winter shutdown
For water conservation
Stagnant, standing water promotes corrosion
Scroll down for the answer...
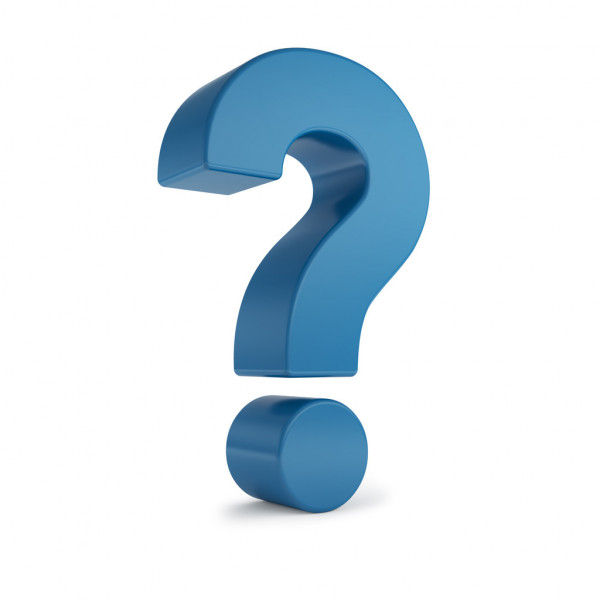
Answer: To inspect the tubes.
The water inside tubes can freeze in winter shutdown
Stagnant, standing water promotes corrosion
We need to remove water from the chiller condenser to minimize corrosion and freezing of water. Draining water allows us to inspect the tubes for a defect.
Question #8: How do we detect defects in tubes of the water-cooled condenser during the seasonal shutdown of the chiller?
By eddy current testing of condenser tubes
By visual inspection of condenser tubes
By ultrasonic testing of condenser tubes
By magnetic particle testing of condenser tubes
Scroll down for the answer...
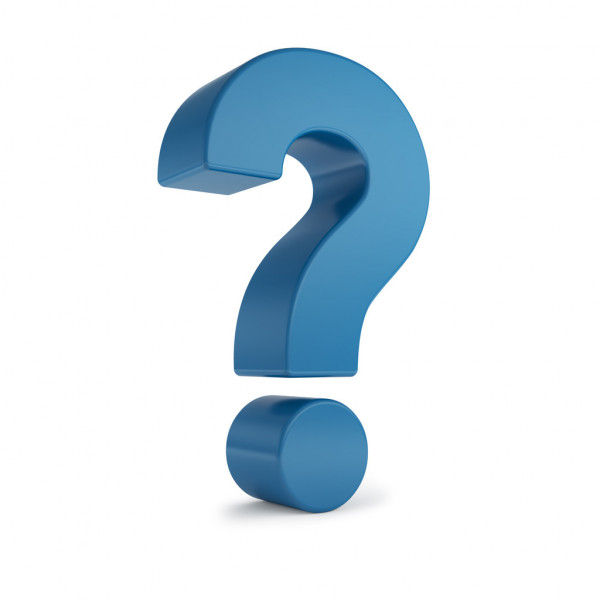
Answer: By eddy current testing of condenser tubes
To protect the long term life cycle of chiller tubes, eddy current testing (ECT) is an accurate means of determining the condition of condenser tubes.
Question #9: How do we interpret eddy current testing results?
By comparing the signals with calibrated results
By measuring wavelength
By measuring frequency
By measuring the time period of oscillation
Scroll down for the answer...
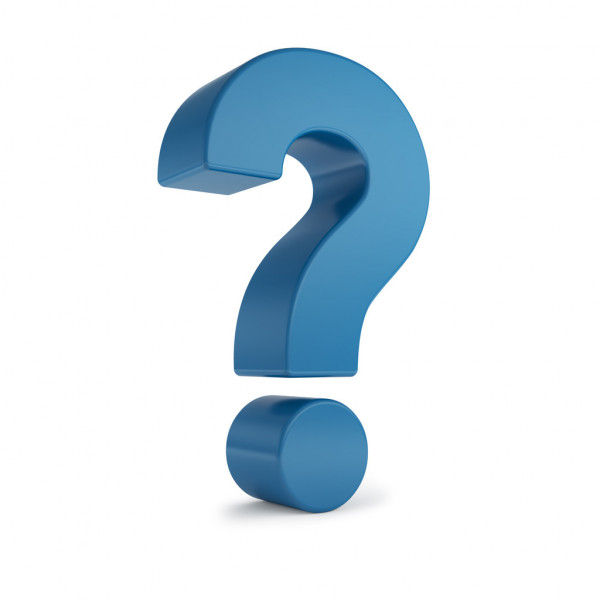
Answer: By comparing the signals with calibrated results
Eddy Current Test signals are compared with calibrated results to interpret test results.
Question #10: Identify the correct order of performing the Eddy Current Test(ECT) from the following.
1. Drain water inside tubes
2. Insert the probe inside each condenser tube along its entire length.
3. Set up an eddy current machine
4. Open an end bell of the condenser tube.
Scroll down for the answer...
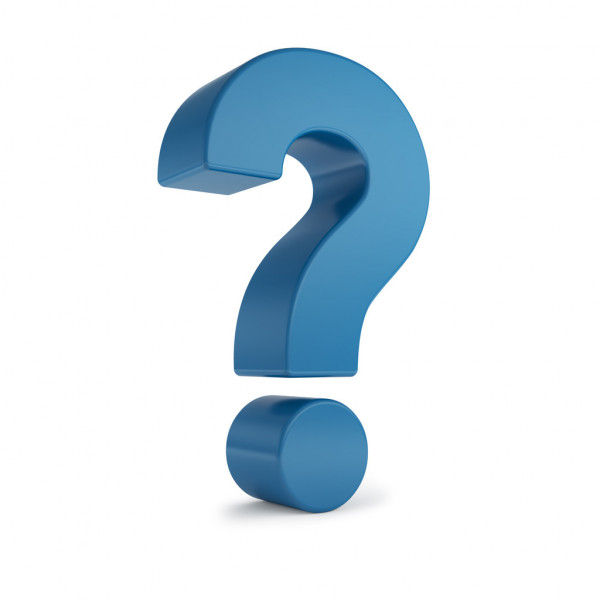
Answer: Drain water inside tubes
Open an end bell of the condenser tube.
Set up an eddy current machine
Insert the probe inside each condenser tube along its entire length.
The correct order is as follows: Drain water inside tubes, Open an end bell of the condenser tube, Set up an eddy current machine, Insert the probe inside each condenser tube along its entire length.
Question #11: A thin layer of dust on the condenser _________ the chiller efficiency.
increases
decreases
does not affect
all the above
Scroll down for the answer...
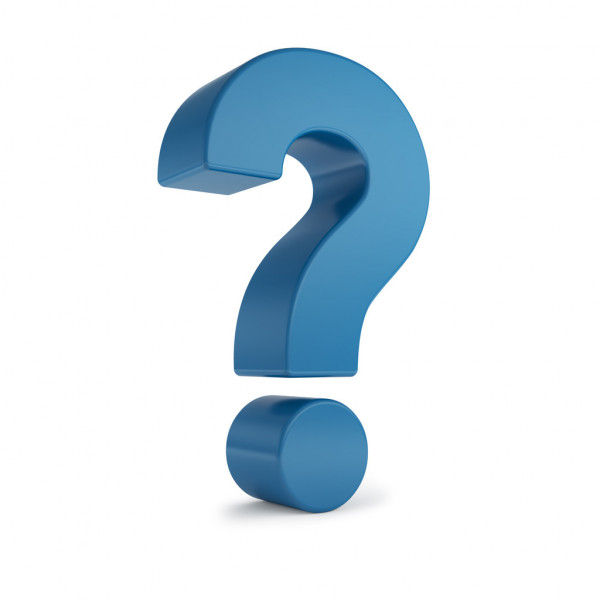
Answer: decreases
A thin layer of dust on the condenser decreases the chiller efficiency.
Question #12: We need to use the same tools for cleaning water-cooled condensers and air-cooled condensers.
True
False
Scroll down for the answer...
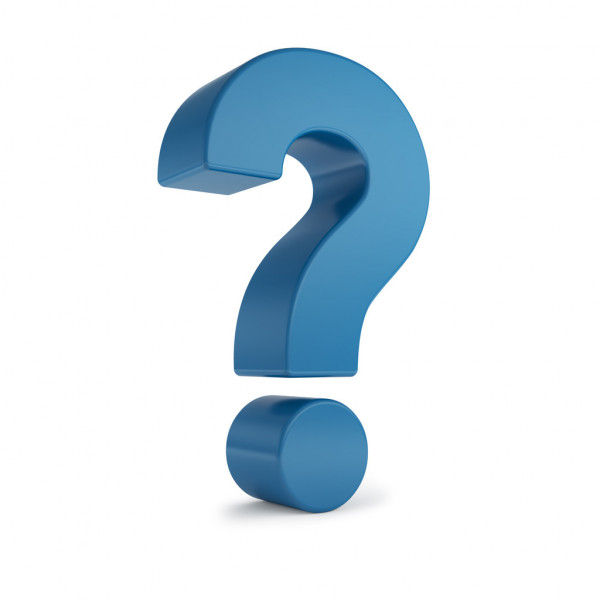
Answer: False
False. We use different tools for cleaning them. We use a rodding machine for a water-cooled condenser and a spray nozzle for an air-cooled condenser.
Question #13: Which of the following components cleaning procedure is the same? (Select all that apply)
Chiller evaporator
Expansion valve
Microchannel condenser
Shell and tube condenser
Scroll down for the answer...
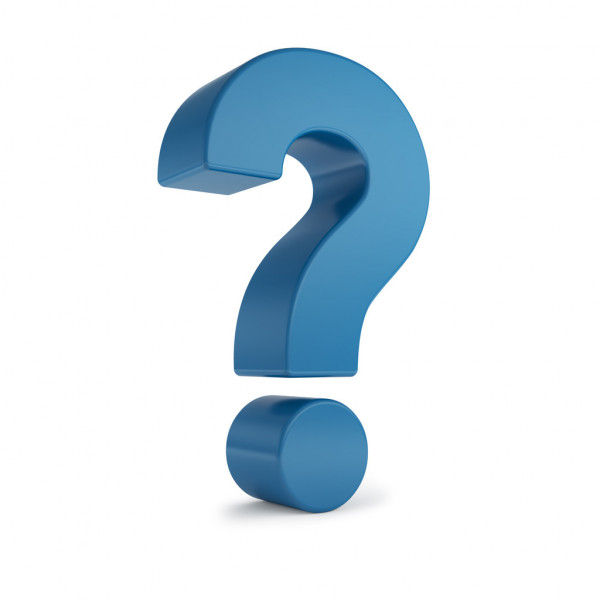
Answer: Chiller evaporator
Shell and tube condenser
We follow the same procedure as shell and tube condenser to clean shell and tube evaporator, but the frequency of cleaning is less.
Question #14: A rodding machine is used to clean the ________.
chiller’s metering device
chiller’s evaporator tubes
chiller’s evaporator fins
chiller’s filter drier
Scroll down for the answer...
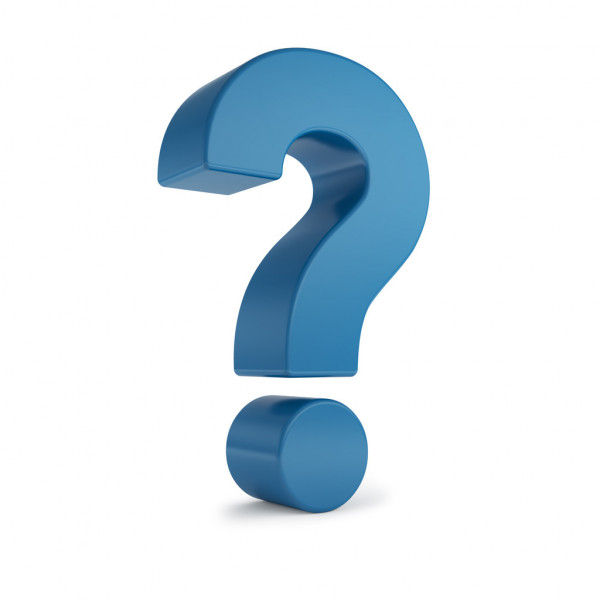
Answer: chiller’s evaporator tubes
A rodding machine is used to clean the chiller’s evaporator tubes.
Question #15: Which type of evaporator is used in a chiller system?
Expansion valve
Microchannel evaporator
Shell and tube evaporator
Finned tube evaporator
Scroll down for the answer...
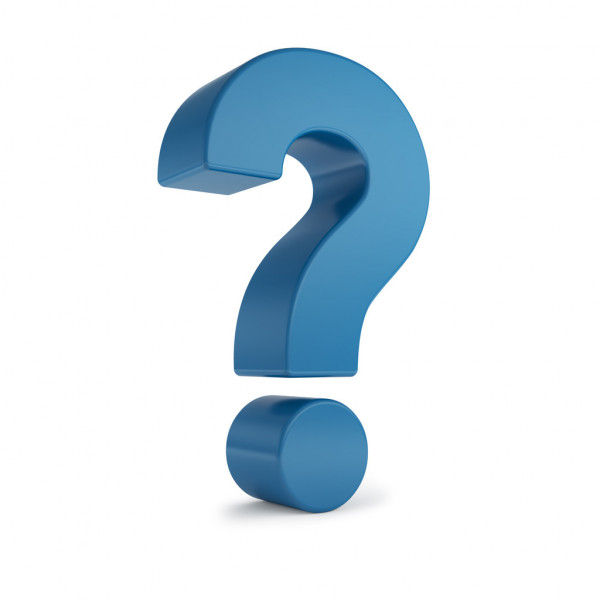
Answer: Shell and tube evaporator
Chiller systems usually contain a shell and tube type of evaporator.
Other References: