Job Site Risks
- SkillCat Team
- Apr 1
- 6 min read
Safety Basics: Chapter 2
In this module, we will talk about the following job site risks:
- Fall,
- Fire, and
- Electrical risks
We will also review important safety protocols. Skip to quiz!
Fall Risk
The Occupational Safety and Health Administration (OSHA) standard says that fall hazards occur when employees fall from six feet or more above the ground. These fall hazards are more likely to happen when safety protocols are not followed or when we are not aware of what protective equipment to use.
An example of a common fall risk at HVAC job sites is when workers fall from the rooftop of a building while installing rooftop units. This can happen when personal fall arrest systems are not used or ladders are misused.
A personal fall arrest helps protect you when working above ground. Between 1982 and 2015, about 54% of workers at construction sites were killed because they had no access to a personal fall arrest system! In addition, 23% of workers had access to a personal fall arrest system but did not use it.
A personal fall arrest includes a body harness that you wear connected to a lanyard. The lanyard is a flexible line of rope, wire rope, or strap. The lanyard is important because it connects your body harness to an anchorage so that you do not crash to the ground when working from heights.
An anchorage is a secure point of attachment for equipment such as lanyards. In order to set a strong anchor point, it should be set on a firm support, such as steel, because it needs to hold your weight. Using plumbing ductwork or pipe vents for anchorage is dangerous because they might not be secure.
Setting strong ladder anchors are also essential to prevent fall risks at work. Ladder anchors help prevent the ladder from moving sideways based on your weight. In addition, the ladder should be set on a firm, level surface so that it is stable enough for you to climb.
When using ladders, we need to be sure that the ladder is not damaged or missing any parts. A ladder should not be used if it:
is broken or bent,
has loose nails, bolts, or screws, or
contains oil, grease or slippery materials
Fire Risk
A fire risk is the likelihood of a fire occurring and the consequences if a fire should occur. If the fire hazards on a job site are not properly managed, a fire could break out. This can have devastating consequences for both the property and the workers.
There are 6 classes of fire:
Class A - fires involving solid materials such as wood
Class B - fires involving flammable liquids such as oils
Class C - fires involving electrical equipment
Class D - fires involving combustible metals such as magnesium
Class K - fires involving cooking oils and fats
Another type of fire extinguisher is a fire blanket. It is mostly used on hot oil fires, such as frying pans or small deep fat fryers. They can also be used on someone whose clothing catches on fire.
Electrical Risk
An electrical risk at work is injury caused directly or indirectly by electricity that can cause death to a worker. The most common electrical hazards occur from high voltage overhead power lines. Coming in contact with power lines can cause you to get shocked!
When you experience an electrical shock, it feels like an instant jerk. Your muscles tighten up, making it impossible for you to pull away from the circuit. Electric currents above 10 milliamps cause severe shock, in which your lungs constrict, and it becomes hard to breathe.
Lockout tagout is a procedure used to make sure that equipment is shut down and tagged before working on its maintenance. It is used to prevent people from working on machines that may injure them.
In order to protect ourselves at work from electrical hazards, we should make sure that we are using proper equipment. For example, damaged tools should be repaired or replaced. We should also maintain at least 10 feet from overhead power lines to avoid major burns or electrocution.
Job sites can have fall, fire, and electrical risks. In order to keep ourselves safe, we need to be careful of our surroundings and follow safety protocols. We should also use the proper equipment in order to prevent injury or death to ourselves and our coworkers.
Question #1: OSHA standard says that fall hazards happen when employees fall six feet or more above the ground.
True
False
Scroll down for the answer...
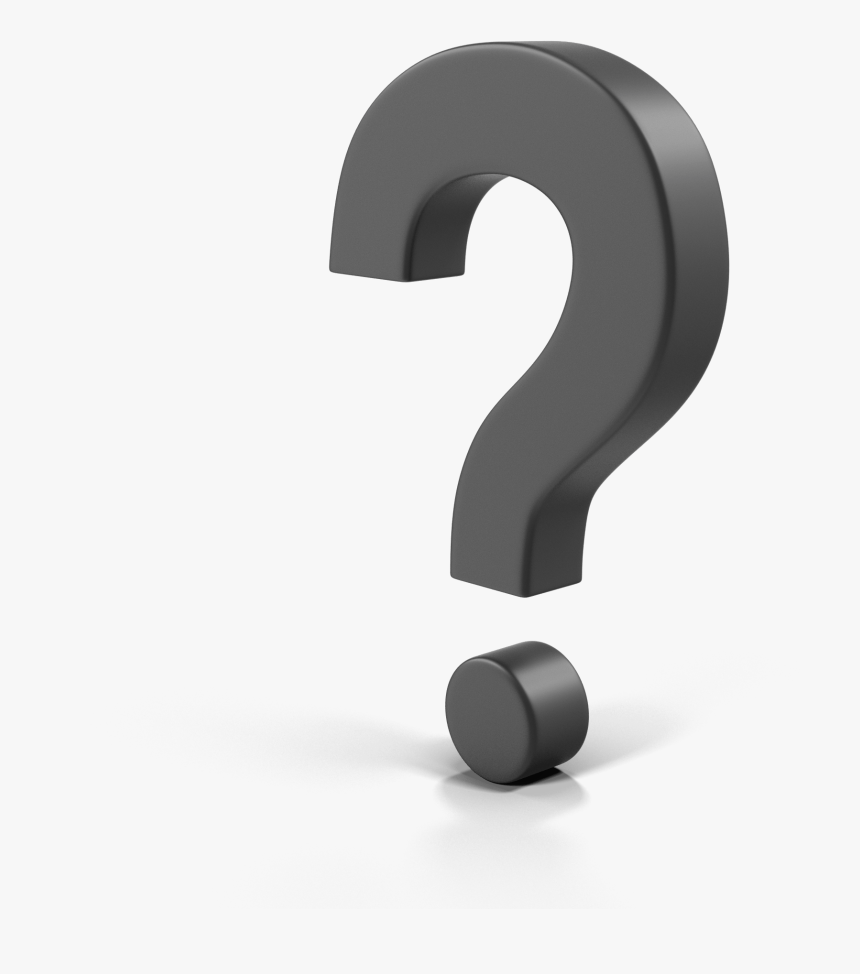
Answer: True
True! The OSHA standard says that fall hazards happen when employees fall six feet or more above the ground.
Question #2: Which of the following is true about setting strong anchor points?
Anchor points such as plumbing ductwork are preferred because they can sustain a lot of weight.
Anchor points such as plumbing ductwork are preferred because they are not secure.
Anchor points such as steel are preferred because they can sustain a lot of weight.
Anchor points such as steel are preferred because it is weak.
Scroll down for the answer...
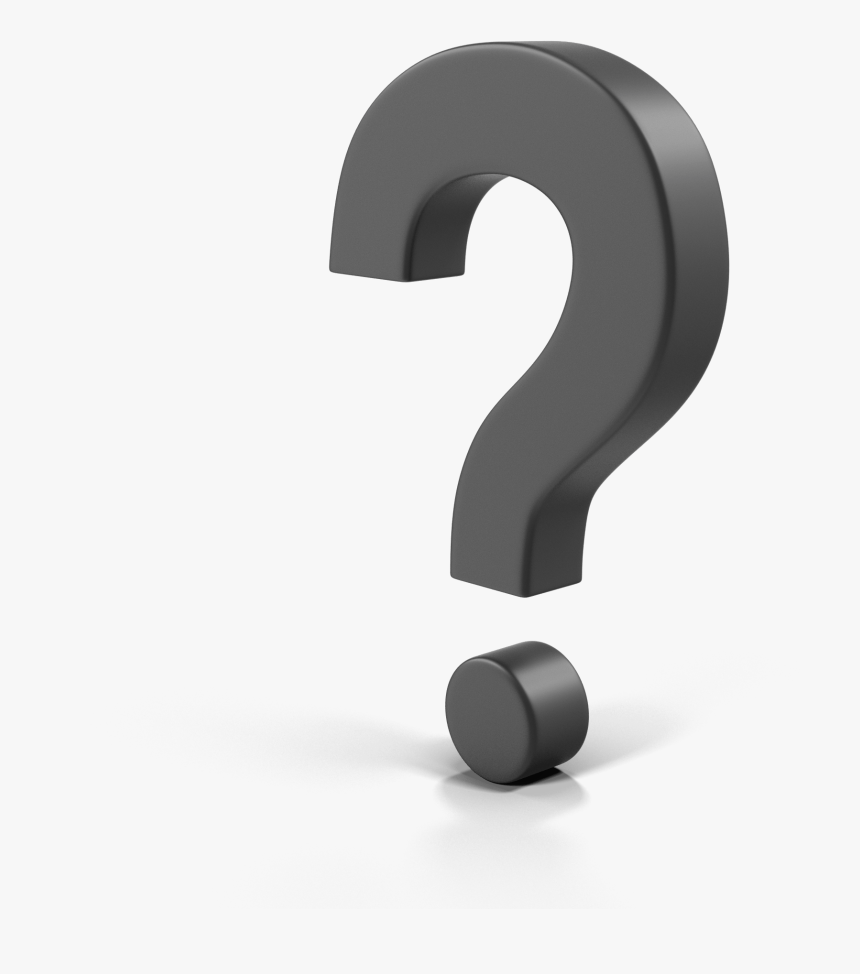
Answer: Anchor points such as steel are preferred because they can sustain a lot of weight.
An anchor point, such as steel, is preferred. Steel is able to sustain a lot of weight, including your body weight. This is important so that you do not fall from heights while working!
Question #3: It is important to set the ladder on a firm, level surface so that it is shaky and unstable as you climb up it.
True
False
Scroll down for the answer...
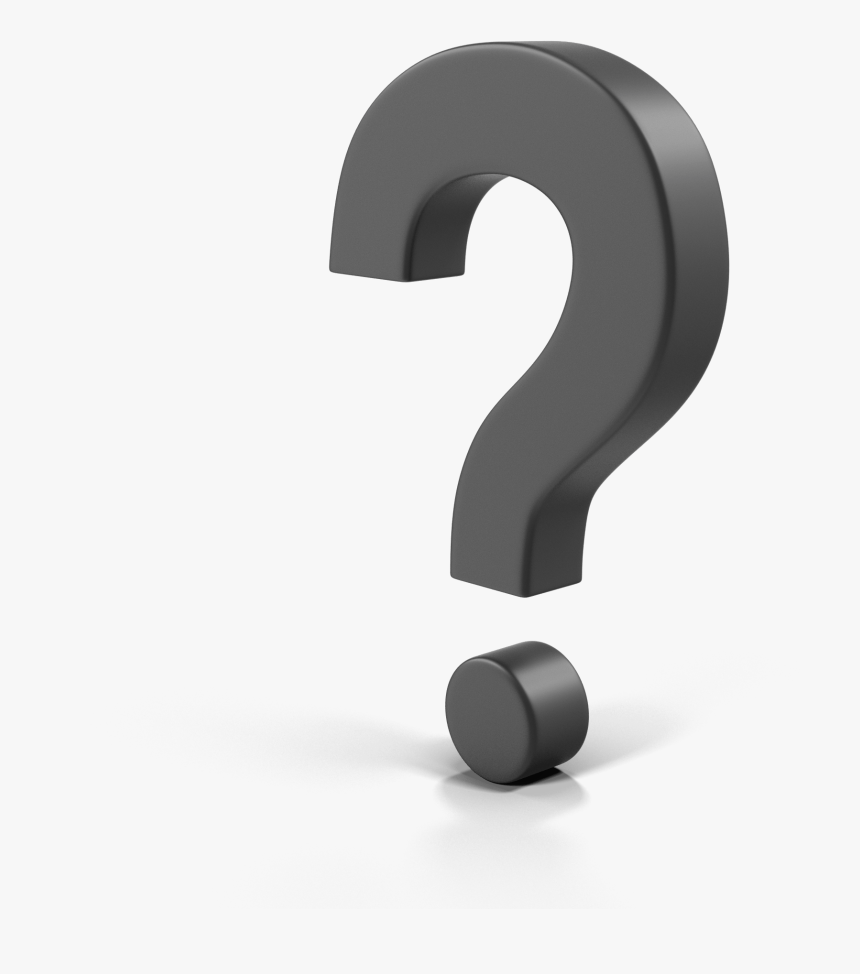
Answer: False
False! You want to set the ladder on a firm, level surface so that it is stable for you to climb.
Question #4: According to OSHA rules, how many points of contact should you maintain while climbing a ladder?
One
Two
Three
Four
Scroll down for the answer...
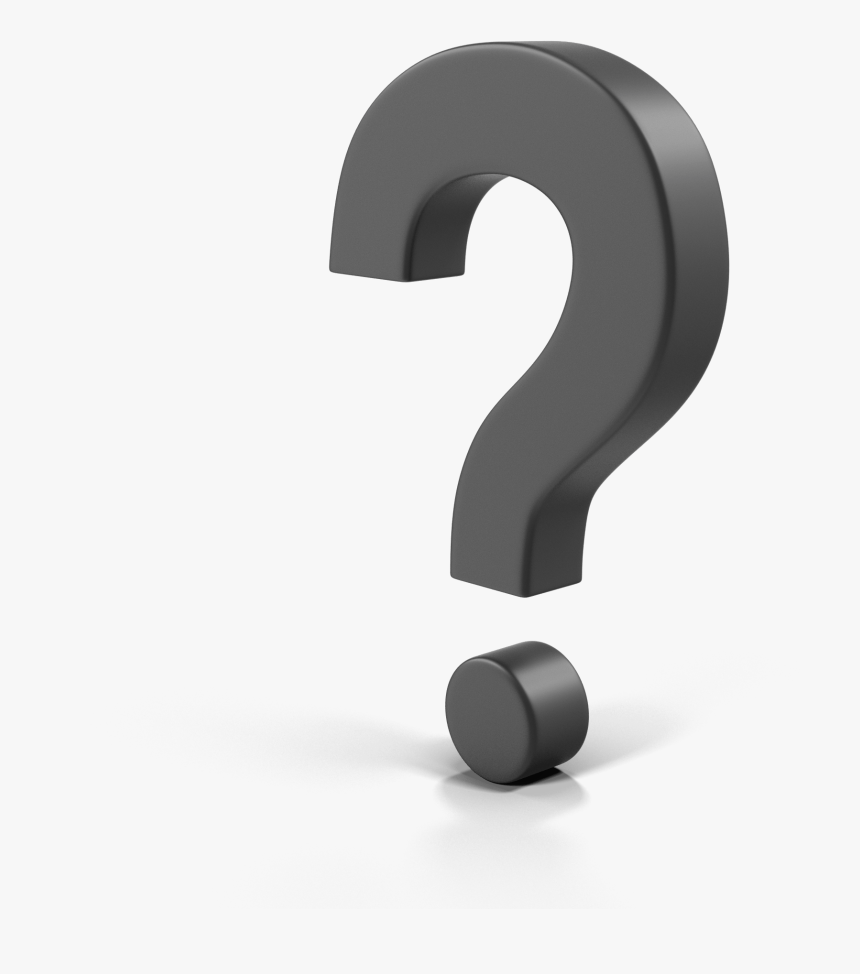
Answer: Three
According to OSHA rules, you should maintain three points of contact while climbing a ladder.
You should not carry anything up while climbing the ladder.
Question #5: Which of the following is NOT a common fall hazard?
Unprotected fall holes and wall openings
Improper scaffold construction
Unguarded, protruding steel rebars
Proper use of portable ladders
Scroll down for the answer...
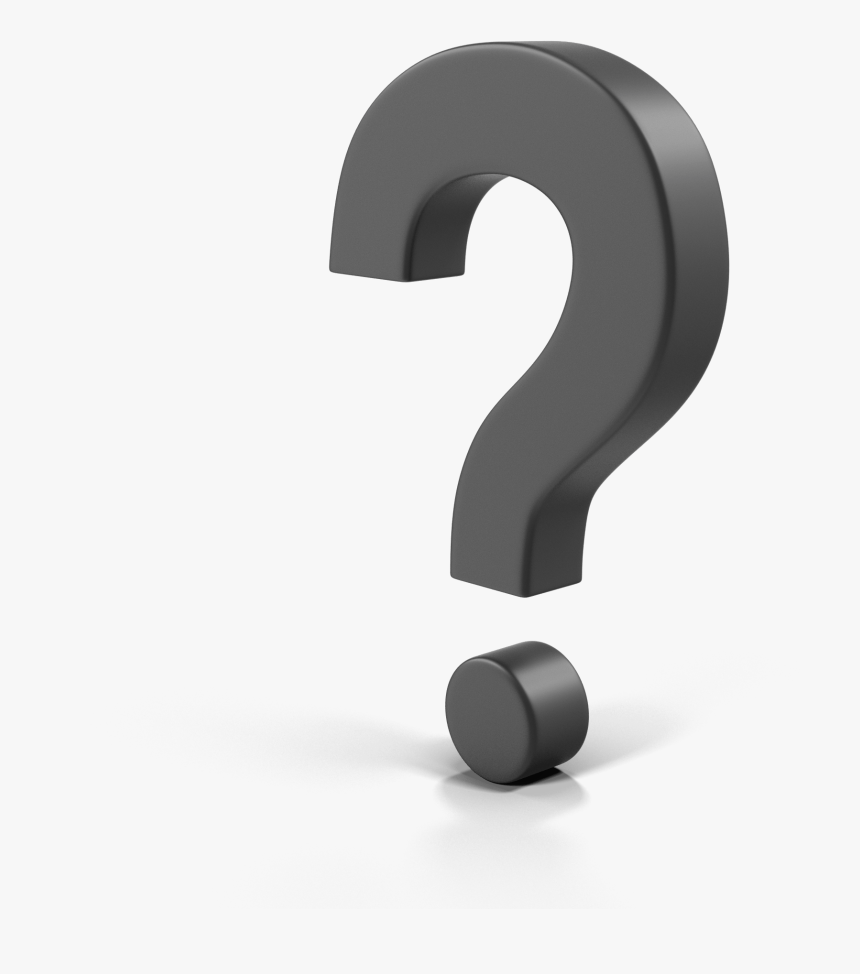
Answer: Proper use of portable ladders
The proper use of portable ladders is not an example of a common fall hazard. However, misuse of portable ladders is a common fall hazards.
Question #6: Which type of fire extinguisher is correctly paired with its class of fire?
Class A - flammable liquids
Class B - ordinary combustibles
Class C - electrical equipment
Class D - cooking fats
Scroll down for the answer...
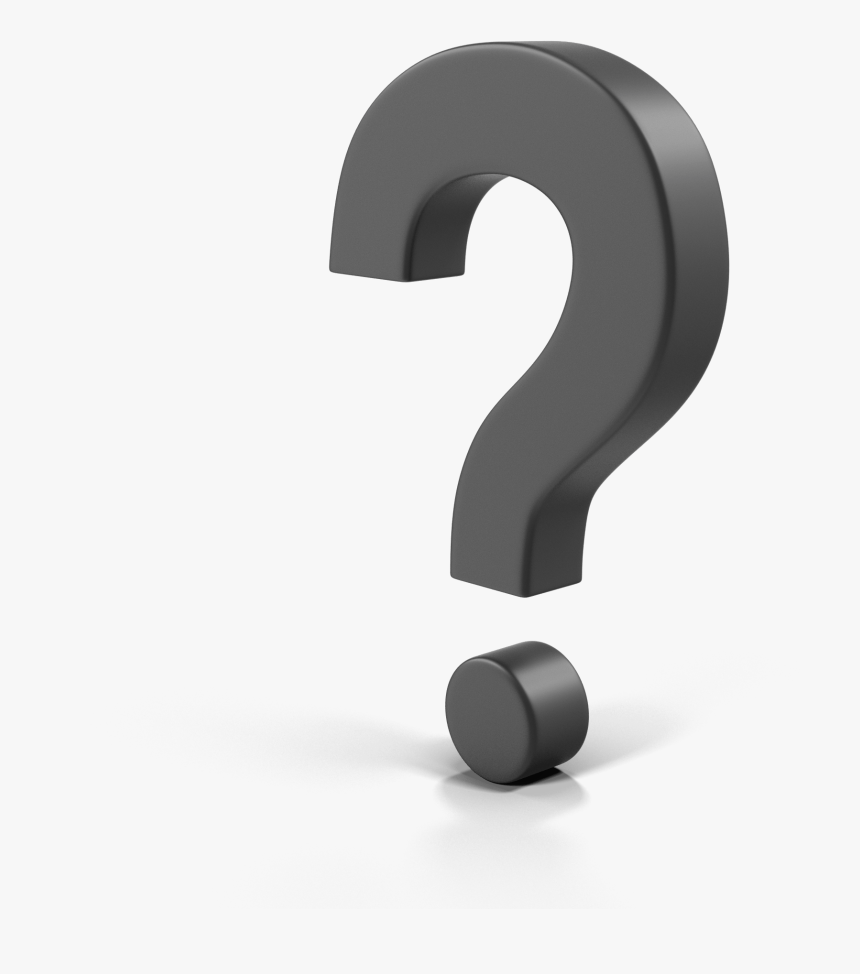
Answer: Class C - electrical equipment
Class C fire extinguishers contain carbon dioxide and can be used for electrical equipment.
Question #7: What does the acronym PASS stand for?
Pull, Aim, Squeeze, and Sweep
Pull, Aim, Sweep and Squeeze
Push, Aim, Sweep and Squeeze
Push, Aim, Swap, and Seal
Scroll down for the answer...
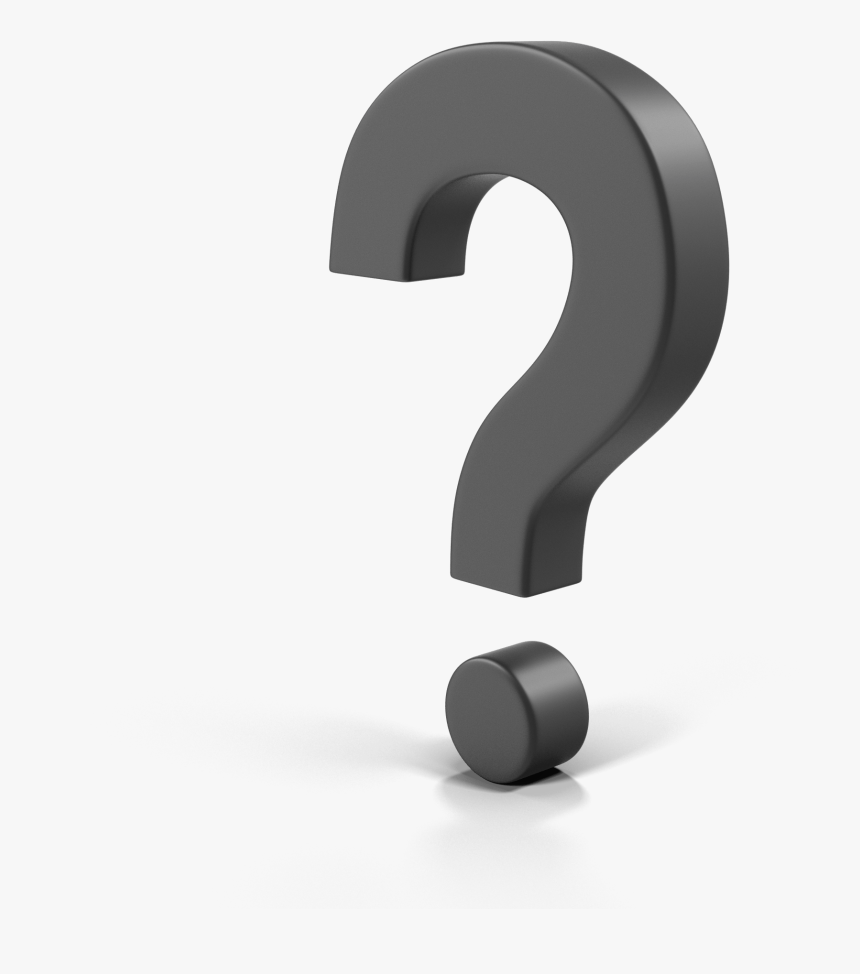
Answer: Pull, Aim, Squeeze, and Sweep
The acronym PASS stands for Pull, Aim, Squeeze and Sweep. Pull the pin to unlock the fire extinguisher and aim at the base of the fire. Squeeze the extinguisher level to discharge content and sweep the hose back and forth until the extinguisher is empty.
Question #8: Smoking is allowed at job sites.
True
False
Scroll down for the answer...
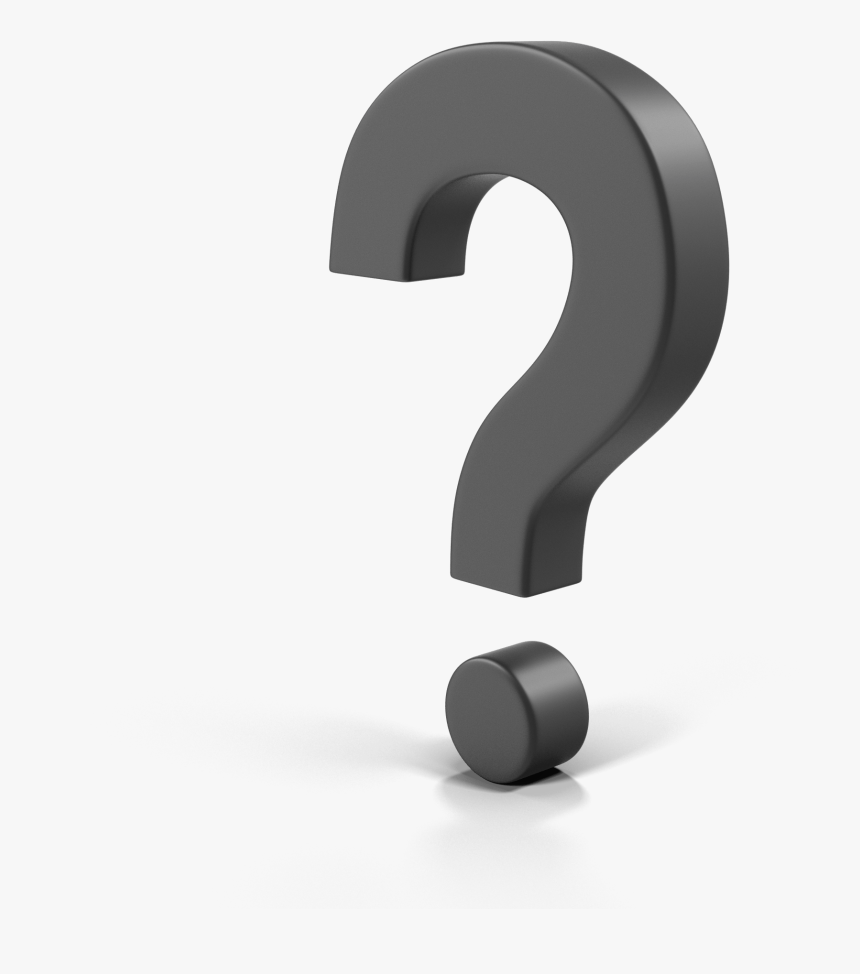
Answer: False
False! Smoking is not allowed at job sites because it presents a serious fire risk.
Question #9: Which of the following is an example of working safely with electrical equipment?
Make sure the equipment is not damaged and safe to use
Continue to use equipment even if it is damaged because you need to get the work done
Do not label equipment as damaged because someone else will do it
Clean equipment even when it is still plugged in
Scroll down for the answer...
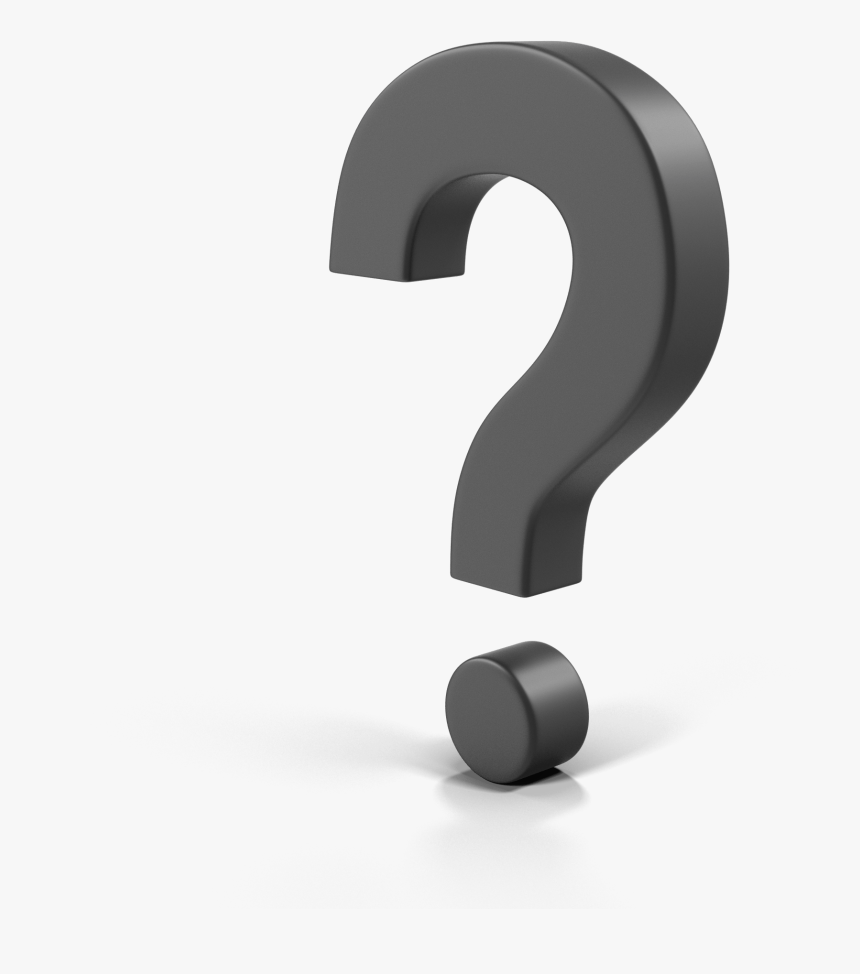
Answer: Make sure the equipment is not damaged and safe to use.
Before using any electrical equipment, you should make sure that it is not damaged and safe to use. If it is damaged, do not use it! Label it as faulty and report it to the technician.
Question #10: What is an example of a way to protect ourselves and avoid electrical risks?
Stand right underneath power lines.
Repair or replace damaged tools.
Use damaged equipment.
Maintain at least one foot from overhead power lines.
Scroll down for the answer...
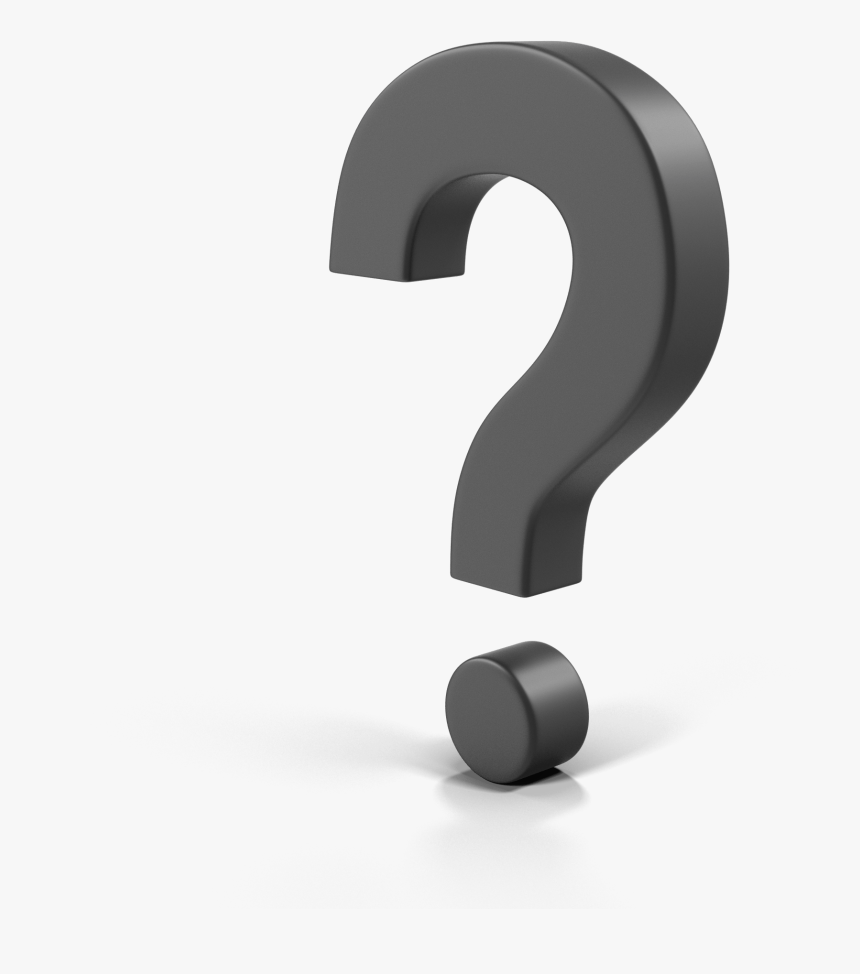
Answer: Repair or replace damaged tools.
It is important to repair or replace damaged tools to avoid electrical risks.
Question #11: What is an example of how you can avoid slips, trips and falls at work?
Keep walkways clear at all times
Not wearing any PPE
Being distracted by texting on our cellphones
Running up and down the stairs as often as possible
Scroll down for the answer...
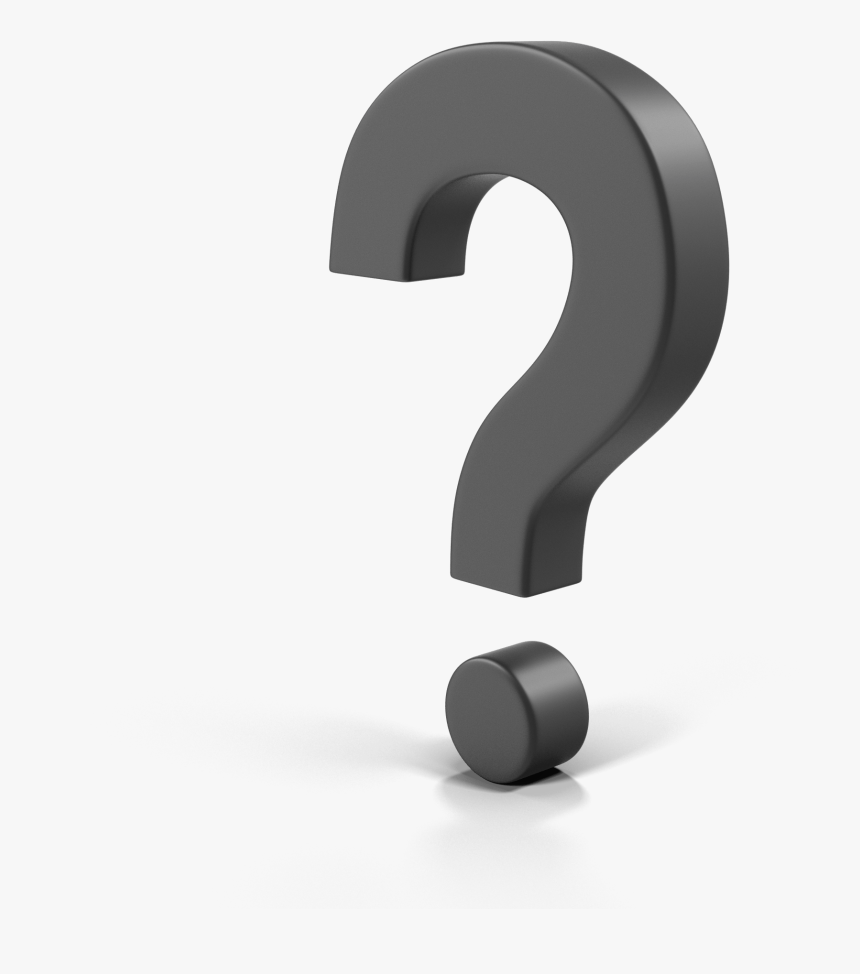
Answer: Keep walkways clear at all times
You should maintain a neat and tidy work area. Keep walkways clear at all times to prevent you and your coworkers from slipping, tripping, or falling due to unnecessary items blocking the hallway.
Other References: