Visual Inspection
- SkillCat Team
- Mar 27
- 4 min read
Chiller Systems: Routine Maintenance: Chapter 1
Visual Inspection
In this module, we will take a look at the visual inspection of the chiller systems. Skip to quiz!
Introduction
Visual inspection is the oldest and most basic method of inspection. We inspect the equipment with our naked eyes. It does not require any special equipment for the inspection. We can detect scratches, dirt, foreign matter, and other appearance defects during visual inspection.

Visual inspection is more cost-effective compared to other methods. It is the easiest and most reliable inspection.
Visual inspection takes place with a technician walking around plants like the chiller system and visually inspecting every single part of it. A well-trained technician can detect most of the problems through visual inspection.
During visual inspection, we check for
Leaks,
Vibration,
Noise,
Tightness, and
Cleanliness.
Note that visual inspection is not limited to the above points only.
Leaks

If we find somewhere in the chiller system with water or oil traces, probably that is the leakage point. Some obvious places to look for leaks in the chiller systems are service valve caps, brazed fittings, and piping joints.
Vibration and Noise
Vibration and noise are usually addressed together because they are closely related. Noise is often a consequence of the vibration. Some technicians only focus on noise and use plenty of soundproofing. This is not the best approach since it does not solve the root cause.
Some vibration and noise are common even in a correctly installed and well-maintained chiller system. This is because the chiller system contains many moving parts. However, excessive vibration and noise can lead to other performance issues.
Recall that vibration is simply a back and forth movement or oscillation of components in motorized equipment. Eliminating vibration completely is not possible, but it can be reduced and isolated to a point where its effects are negligible.
The best way to control vibration is to prevent it with best installation practices. In the existing installations, it can be minimized with adequate routine maintenance. We install damping pads or spring mounts in chiller systems to reduce vibration.
We have to make sure that the vibration levels of the chiller system are maintained at a minimum. Ensuring the minimum vibration levels will improve the durability of the chiller.
In many cases, most of the noise is produced by the chiller components that are affected by propagated vibration. Noise tells how the chiller system is operating. Keeping noise levels to a minimum will help create an environment that is safer for people’s hearing.
Compressors are major source of noise in the chiller systems. They generate moderate to loud levels of noise depending on the
load of the chiller system, and
size and type of compressor used.
Centrifugal type of compressors is least noisy, followed by the reciprocating, scroll, and screw.
Condenser fans are the second major noise-generating component in the air-cooled chiller systems. This is because condenser fans move a lot of air. Water-cooled chillers of the same capacity as air-cooled chillers generate comparatively less noise because of the absence of condenser fans.
Tightness

We have to inspect all the electrical and mechanical connections to ensure they are secure and tight. This inspection includes all the electrical terminations and mechanical fittings. We need to tighten the connections if necessary.
All the bolts, nuts, and screws in the piping fittings should be tight in order to retain refrigerant or water in the chiller systems. We need check all the bolted connections with wrenches for tightness.
Cleanliness
We have to make sure that the chiller systems and the surroundings are clean. It is recommended that chiller systems to be cleaned if they are dirty. Regular cleaning will lower the operating costs and will also prolong the life of all the parts of the chiller systems.
Visual inspection is the oldest and most basic method of inspection. It is the easiest and most reliable inspection. A well trained technician can detect the most of the problems through visual inspection.
Question #1: During the visual inspection, we inspect the equipment with ______.
Magnifier
Naked eyes
Multimeter
Thermometer
Scroll down for the answer...
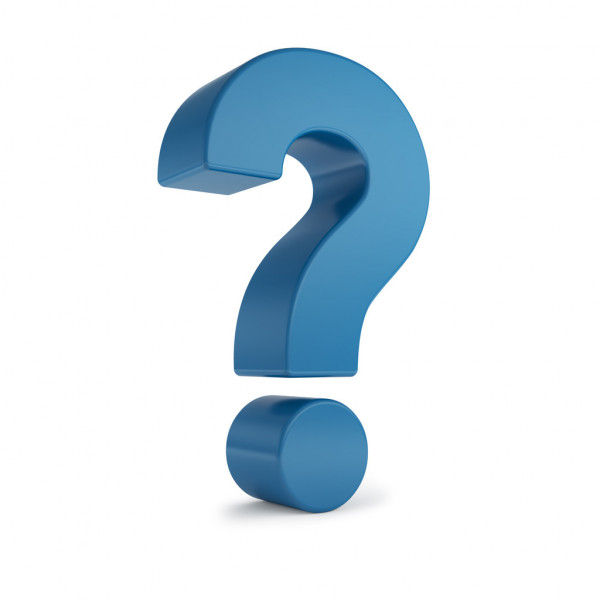
Answer: Naked eyes
During the visual inspection, we inspect the equipment with naked eyes. We are not required to use any special tool for visual inspection.
Question #2: Which of the following are obvious places to look for leaks in the chiller systems?
Piping fittings
Brazed fittings
Service valve caps
All the above
Scroll down for the answer...
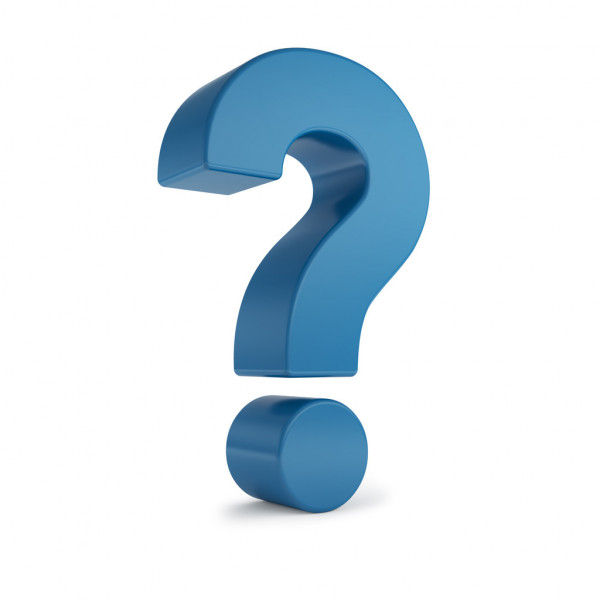
Answer: All the above
Some obvious places to look for leaks in the chiller systems are service valve caps, brazed fittings, and piping joints.
Question #3: ______ is often a consequence of the _______ in the chiller systems.
Vibration; noise
Noise; vibration
Noise; refrigerant
Vibration; water
Scroll down for the answer...
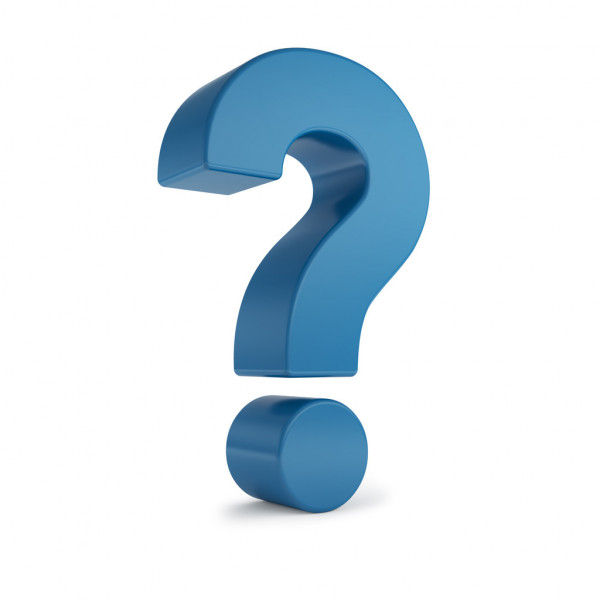
Answer: Noise; vibration
Noise is often a consequence of the vibration in the chiller systems.
Question #4: Which of the following type of compressors is the least noisy comparatively?
Scroll
Reciprocating
Screw
Centrifugal
Scroll down for the answer...
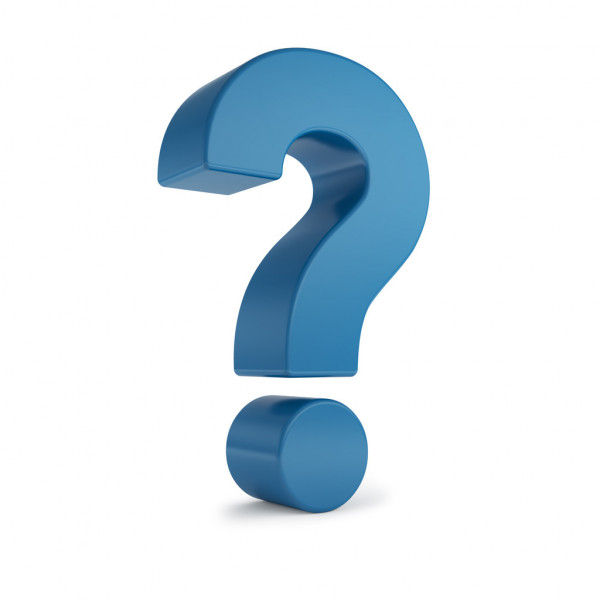
Answer: Centrifugal
Centrifugal type of compressors is least noisy, followed by the reciprocating, scroll, and screw.
Question #5: Which of the following is the second major noise generating components in the air-cooled chiller systems?
Condenser fans
Cooling towers
Compressors
Metering device
Scroll down for the answer...
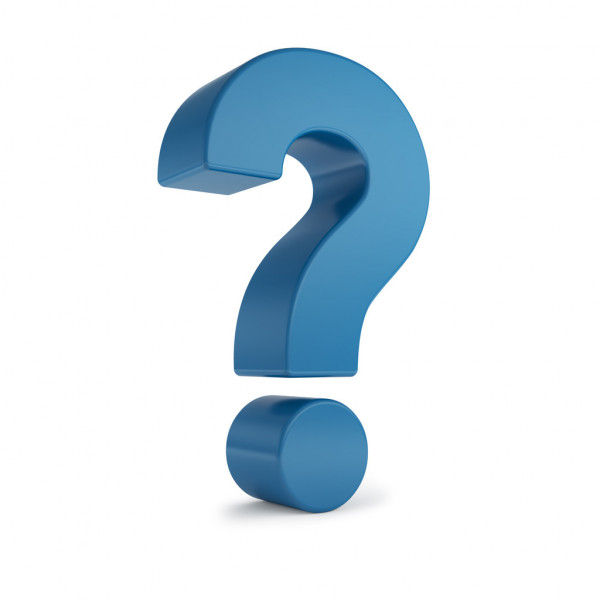
Answer: Condenser fans
Condenser fans are the second major noise generating component in the air-cooled chiller systems.
Question #6: Which of the following are used to check the tightness of the bolted connections?
Screwdrivers
Magnehelic gauges
Wrenches
Hammers
Scroll down for the answer...
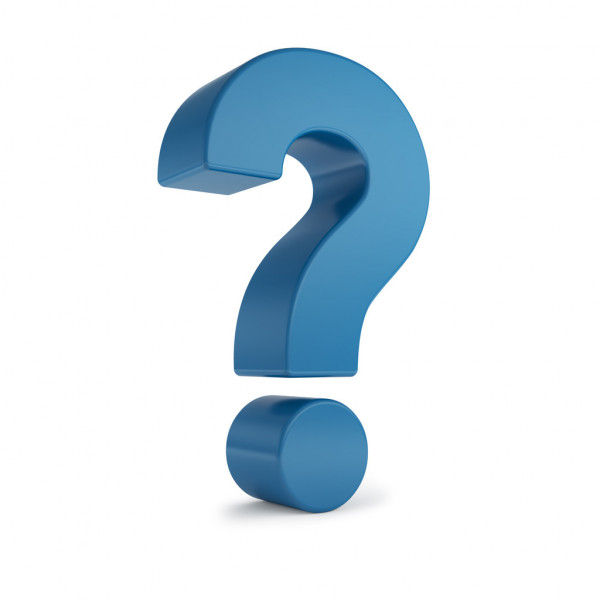
Answer: Wrenches
Wrenches are used to check the tightness of the bolted connections.
Question #7: Regular cleaning will lower the ______ and will also increase the_______ of the chiller systems.
lifespan; operating costs
operating costs; lifespan
refrigerant amount; cooling
cooling; refrigerant amount
Scroll down for the answer...
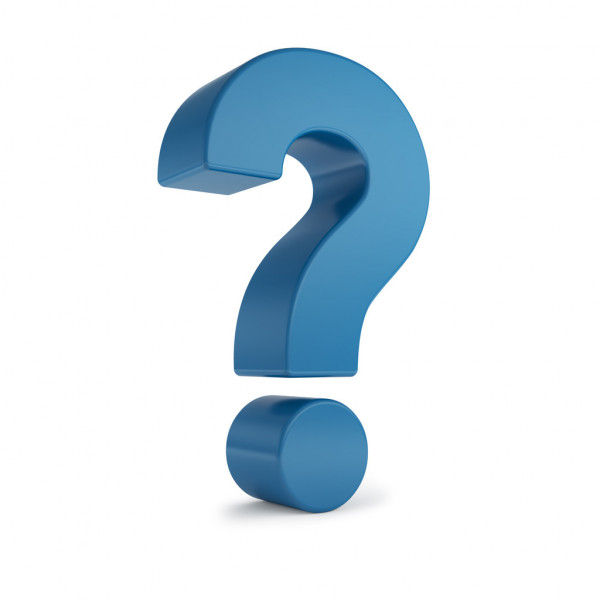
Answer: operating costs; lifespan
Regular cleaning will lower the operating costs and will also increase the lifespan of the chiller systems.
Other References: